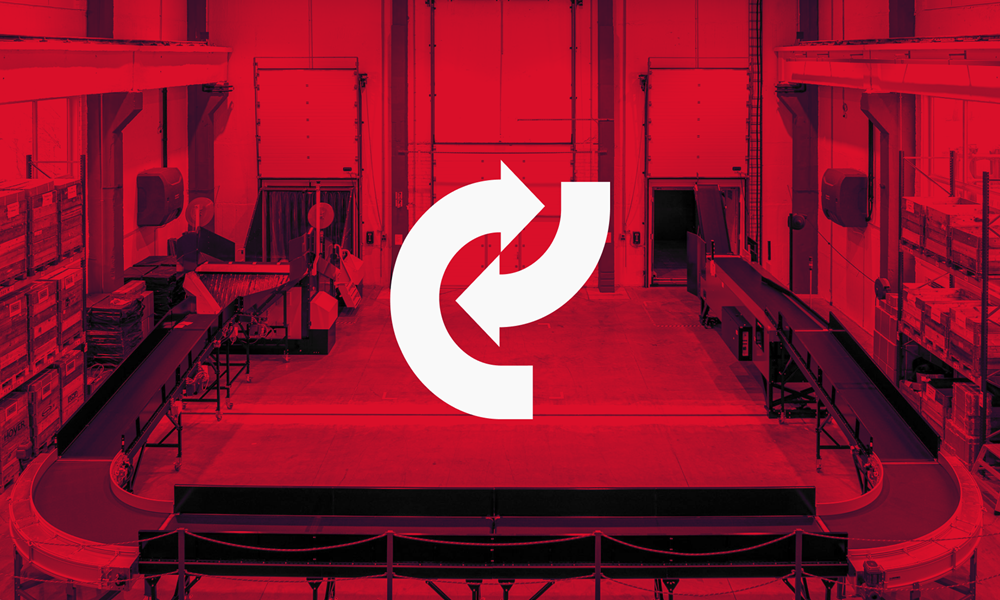
Clients can now test our solutions in modern Technology centres in the U.S., Latvia & Germany
To support customers in making informed decisions about logistics automation, we’ve recently opened three new Technology Centres at our production facilities in the U.S., Latvia and Germany. These centres offer both existing and potential customers the opportunity to experience Caljan solutions in real working conditions.
“The new centres are a strategic investment in deepening customer partnerships and driving collaborative innovation. By providing a tailored environment where customers can explore and test our logistics automation solutions, we enable them to not only assess efficiency and performance but also co-develop solutions that align with their evolving operational needs. This hands-on engagement strengthens our ability to understand customer challenges, accelerate innovation, and deliver automation solutions that create long-term value,” says Derek Wright, Vice President of Group Sales & Marketing.
Each Technology Centre offers different solution demos that support the local market requirements. Customers can see the Caljan AutoLoader and Performer telescopic conveyor with ErgoRider in action at the U.S. centre the AutoLoader and AutoUnloader in Latvia and the Classic telescopic conveyor showcasing the unloading process, along with the AutoLoader and our labeling technologies, at the latest centre in Germany. The new facilities also serve as training areas for our and our clients’ teams to get acquainted with the latest developments and explore the full potential of logistics automation technology.
What sets our Technology Centres apart is the ability to conduct personalised demonstrations: customers can schedule a time to visit us and test how our equipment handles their specific requirements for different parcel sizes and weights. All centres also offer a remote visit experience using Google Lenses to allow larger groups of customers to follow the demonstration from the comfort of their location. This helps them to evaluate the automated products’ performance, integration capabilities, and efficiency in a setting that closely mirrors their day-to-day operations.
But the product showcase and training aren’t the only purpose of these hubs. They are also used as service centres for equipment upgrades that can’t be done onsite at the customer’s site.
The first customers to explore our new centres have already shared valuable feedback. They’ve highlighted how beneficial it is to experience our solutions in action, gaining a clear understanding of how automation can streamline their operations, reduce manual workload, and improve throughput. This input also allows us to understand what other solutions would be good to have at the centres in the future.